Factory automation initiatives are now benefiting from a variety of technologies and enablers.
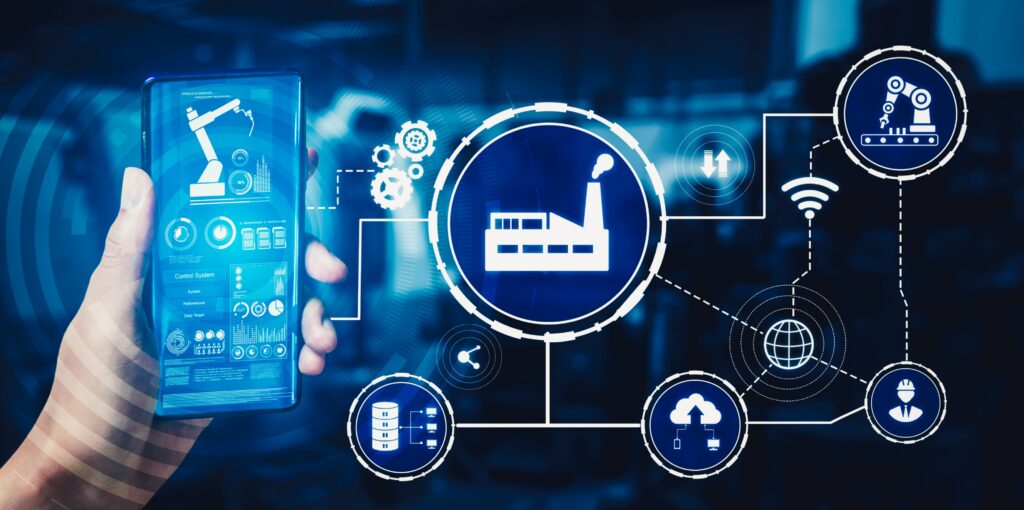
Automation has a long history and has played an important role in all industrial sectors. Industrialization is defined as repeatable high-quality manufacturing in large quantities. The level of automation in the production process has a direct impact on the cost of the finished product.
Continuous developments in automation result in mechanical perfection. That perfection, in turn, depends on control. Manufacturers must strike a compromise between the technologies required to apply control at this level and commercial considerations. These comprise the costs of development and deployment (capital expenditure) and the ongoing cost of execution (operational expenditure).
New technologies can have an impact on industrial automation if producers align capex and opex while appropriately estimating total cost of ownership. This article looks at various technologies that fit this condition as well as some that may have an impact on the future of automation.
Technologies Helping in Industrial Automation
Several technologies, along with their enabling features, are currently having an impact on industrial automation. The competitive advantage of the Industrial Internet of Things (IIoT) will grow as these technologies become more widespread.
- Single-pair ethernet
- Edge Computing
- Time Sensitive Networking.
Single-pair Ethernet
Wide area networking (WAN) has transformed all aspects of modern life. Consumers may access the internet from anyplace, including transatlantic travel. Its application in IIoT means that information and operational technology are merging, and the way connectivity is used is continually evolving. Different elements of the ecosystem are at varying phases of the IIoT journey.
The industrial sector is now largely in agreement on the deployment of Ethernet to support an IP architecture. In addition, single-pair Ethernet (IEEE 802.3cg) is gaining use in industrial automation. The automotive market’s adoption of single-pair Ethernet (SPE) simplifies the physical network. It provides both data and electricity on the same two lines, speeds of 10 Mbps, distances of 1000 meters, and support for multidrop configuration.
The advancement of SPE is helping to bring Ethernet into an environment where single-pair connectivity has long been the chosen approach. SPE’s importance will rise as support develops. The advanced physical layer (APL), developed by industrial leaders, is one example of this. Ethernet-APL makes use of the 10BASE-T1L component of the standard, as well as additions. Ethernet-APL defines physical layer properties such as power, connections, and cables. The Ethernet-APL layer is also designed for use in hazardous environments.
The Ethernet-APL consortium includes the OPC Foundation, Profibus, FieldComm consortium, and OVDA. The physical layer supports a variety of high-level network protocols, including EtherNet/IP, HART-IP, OPC UA, and Profinet.
Edge Computing
The IIoT brought cloud computing to the industrial floor. Cloud platforms play a key role in data collection, processing, and dissemination to back-office applications. Edge computing brings the power of the cloud directly to the production line.

An edge computing system uses high-performance processors to run cloud-level software on a local device. That device connects directly to the manufacturing machinery. There are a number of reasons why edge computing is popular.
First, it permits some, or all, of the operational data to remain within the organization’s borders. There are valid security reasons for using this strategy. Another purpose is to simply reduce the expense of transporting data around. Another goal is to avoid the latency associated with processing time-sensitive data in a cloud environment.
Second, edge computing creates a controlled environment, allowing manufacturers to have more control over their processes. This work cell architecture may enable distributed and distinct workflows, giving you better control over how assets are delivered. An edge computer can transform a small cluster of machines into a standalone production process that can operate outside of a larger manufacturing environment.
Edge computing is about more than just data security and cloud transmission efficiency. It promotes trends like micromanufacturing and on-demand manufacturing.
Time Sensitive Networking
As the IT and OT networks continue to combine, the demand for time-sensitive networking (TSN) grows. The IEEE Standards Association is developing many profiles for time-sensitive networking in several industries, including industrial automation.
The protocol is intended to allow time-critical packets over an Ethernet network. It achieves this through three processes. The first is a mechanism for prioritizing time-critical Ethernet frames while postponing non-critical frames. Transmission time is one tool used to establish priorities. It also considers the frame length to evaluate whether it can be transmitted without interfering with higher priority traffic. Another approach is to create fault-tolerant networks with several pathways to avoid latency.
Semiconductor makers are currently putting these functions on the chip. Multi-chip systems are transforming into single-chip or system-on-chip products. This will continue in concert with efforts to standardize application protocols.
Expect the cost and difficulty of deploying TSN to decrease rapidly. Not all manufacturers will perceive a benefit or need for TSN, at least not right away. As IIoT dominates the production sector, TSN is anticipated to become more prominent.
Technologies Impacting Factory Automation
Industrial equipment has a lengthy operating life. This means that change may be slower than in other markets. For example, wireless mesh networks are still primarily used to connect sensors in an industrial setting. Wired connectivity remains the leading control method.
However, there is increasing cross-pollination between verticals, which is facilitated by wide area networking. Many of the technologies developed in – or dependent on – IT are finding their way into the OT realm. Some of the prominent and most promising technologies are:
- Digital Twins
- Blockchain
- Microservices
Digital Twins
What are Digital Twins?
The concept of operating duplicate systems, or twins, in distinct contexts dates back to NASA’s early days. A twin can be used to mimic and respond to operational data that is occurring elsewhere, even on another planet. Moving to the digital domain has allowed the notion to become more cost-effective and perhaps more versatile.
Digital twinning entails modeling an action rather than mimicking it. The discrepancy is due to the twin using real-world data. This is where Internet of Things technology comes into play. Sensors are the main source of data.

Digital Twins in Factory automation
As manufacturers install more sensors on industrial equipment and connect them to high-speed networking, the utilization of digital twins becomes more viable.
Recent discoveries indicate that OEMs are implementing digital twins at the work cell level. This makes it easier to model a subset of a system as a function rather than the complete factory.
As edge processing advances, the use of numerous digital twins will become increasingly widespread. As a result, the two are inextricably linked, as edge processing works only locally. Although edge processing does not rely on digital twinning, the synergy is clear.
Blockchain
In the manufacturing industry, the term “blockchain” is often connected with the supply chain. Engineers have been discussing the idea of utilizing blockchain technology to authenticate and trace products in the supply chain for many years.
Part of the potential for IoT adoption stems from the commercialization of information. Trust will be a critical component of success. Using blockchain to give proof of validity could be crucial.
The movement toward offering something as a service is also gaining traction. Blockchain could be used to validate the hardware platform that provides the service. If the service relies on legitimate parts being installed in a system, blockchain could be the most effective method of verifying those parts.
Microservices
If a pattern emerges in the advancement of industrial automation, it could be about making work cells more intelligent. Edge computing, and soon digital twins, are centered on work cells and flexible functionality.
Microservices can be described as software-level modularity. The methodology is currently popular on cloud platforms. A microservice architecture is more agile, scalable, and manageable than huge monolithic software architectures.
The diversity of industrial automation processes suggests that microservices will become more common here as well. Flexibility on the shop floor will allow machines to be repurposed more regularly. Using a microservices strategy will allow for greater flexibility.
AI + Factory Automation
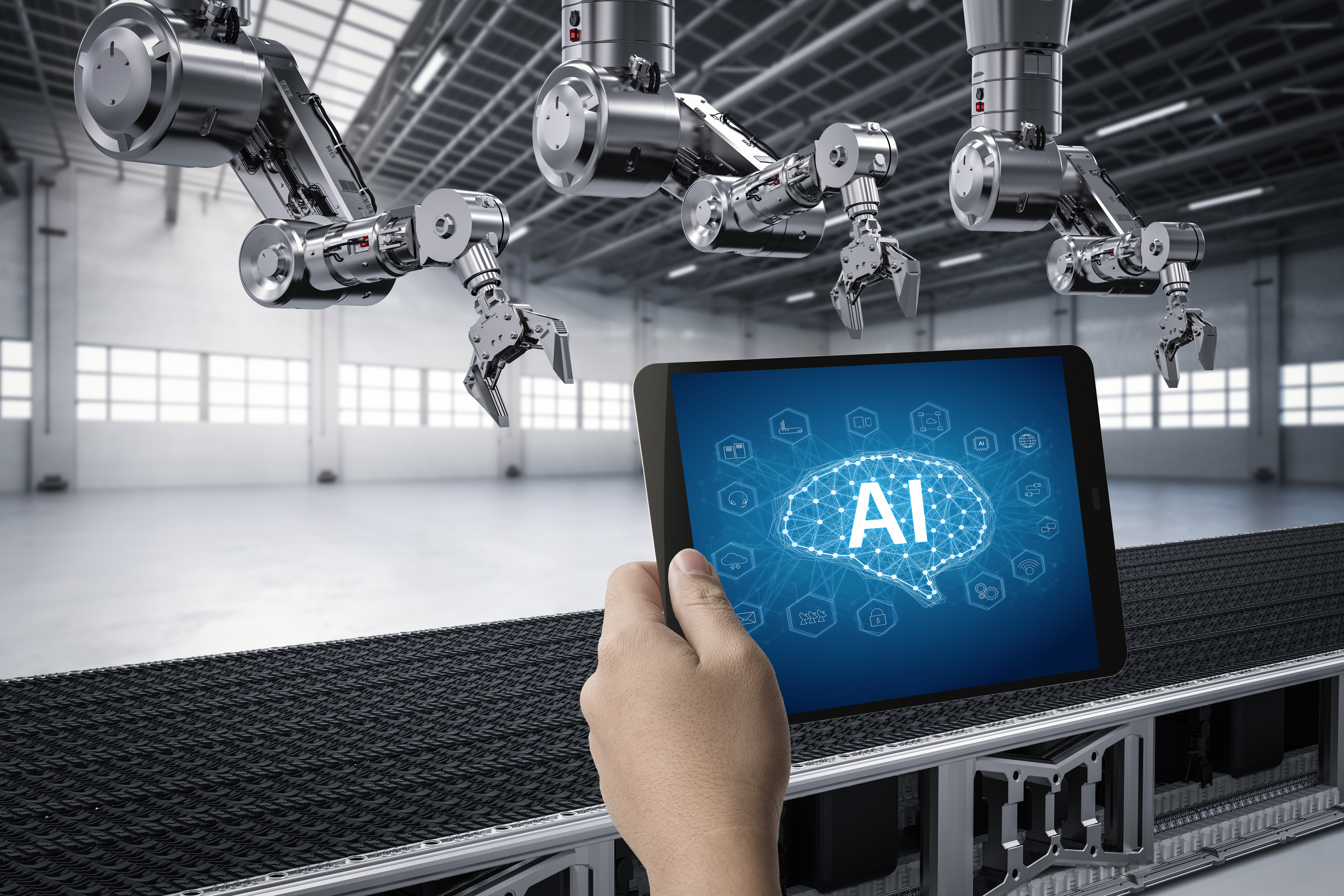
There is considerable potential for AI to influence industrial automation. Current examples of AI show that the technology is capable of following procedures and adjusting to specified parameters. Its true power stems from its ability to respond predictably to unexpected events.
Using AI in this manner should improve procedural operations performed by programmable logic controllers. AI can now write the ladder logic used to configure PLCs. This scenario employs AI in a mechanical manner to augment a function.
Introducing AI into human-centric processes could be the next step. In this case, the AI would have to “think” like an operator. It would initially assist, but might eventually displace the human in the loop.
Conclusion
Industrial automation is continually evolving. New technology, frequently from other market sectors, gives the impetus for advancement. Caution is always advised, but the rate of change appears to be growing.
According to studies, the productivity gap between large OEMs, which can afford to actively incorporate new technologies, and smaller firms is expanding. As access to these technologies improves and the overall cost of ownership falls, this gap may once again narrow.